-
- News
- Books
Featured Books
- smt007 Magazine
Latest Issues
Current IssueBox Build
One trend is to add box build and final assembly to your product offering. In this issue, we explore the opportunities and risks of adding system assembly to your service portfolio.
IPC APEX EXPO 2024 Pre-show
This month’s issue devotes its pages to a comprehensive preview of the IPC APEX EXPO 2024 event. Whether your role is technical or business, if you're new-to-the-industry or seasoned veteran, you'll find value throughout this program.
Boost Your Sales
Every part of your business can be evaluated as a process, including your sales funnel. Optimizing your selling process requires a coordinated effort between marketing and sales. In this issue, industry experts in marketing and sales offer their best advice on how to boost your sales efforts.
- Articles
- Columns
Search Console
- Links
- Events
||| MENU - smt007 Magazine
Alpha to Feature New Material Set Combinations at SMTA Atlanta Expo
April 6, 2017 | Alpha Assembly SolutionsEstimated reading time: 1 minute
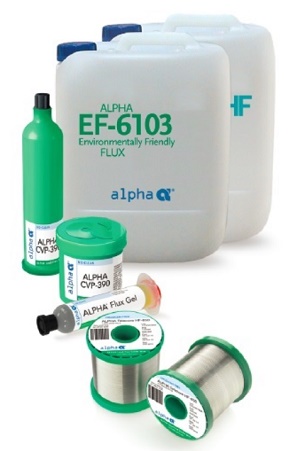
Alpha Assembly Solutions, the world leader in the production of electronic soldering and bonding materials, will feature its new material set combinations at the upcoming SMTA Atlanta Expo to be held April 19th at the Infinite Energy Center.
The material set combinations include paste, tacky flux, cored wire, and wave soldering flux that are tested with one another to achieve greater reliability. “Reliability is a critical issue for our customers, and Alpha has done the testing necessary to demonstrate which material pairings will produce the greatest reliability,” said Rossi English, District Sales Manager for the Southeast. “This relieves the customer from much of the trial and error that occurs with specific electronics assembly processes.”.
Alpha, a part of the MacDermid Performance Solutions group of businesses, will also showcase its portfolio of innovative materials and solutions for the electronics assembly industry, and its ALPHA® Recycling Services capabilities.
About SMTA
The Surface Mount Technology Association (SMTA) is an international network of professionals who build skills, share practical experience and develop solutions in electronic assembly technologies, including microsystems, emerging technologies, and related business operations.
About Alpha Assembly Solutions
Alpha Assembly Solutions, a MacDermid Performance Solutions Business, is the global leader in the development, manufacturing and sales of innovative specialty materials used in a wide range of industry segments, including electronics assembly, power electronics, die attach, LED lighting, photovoltaics, semiconductor packaging, automotive and others.
With a unique global presence in over 30 locations throughout the Asia Pacific, Americas and Europe regions, Alpha supplies a full line of ALPHA® electronics assembly material products, including Solder Paste, Exactalloy® Solder Preforms, Cored Solder Wire Solder, Wave Soldering Fluxes, Bar Solder Alloys, and Stencils. It offers die attach product technologies to the power electronics segment in its Argomax®, Atrox™ and Fortibond™ brands.
For the LED segment, Alpha offers its Lumet™ products covering applications from die attach to systems assembly in the LED manufacturing process. Alpha also offers product technologies for the Photovoltaic segment, including high performance liquid fluxes and solder alloys for producing standard ribbon and bus bar, as well as, solder pastes, cored wire, conductive adhesives and preforms for use in PV module assembly. Also, Alpha’s Advanced Materials unit is the leader in electronic polymers and solder materials for semiconductor packaging applications.
Since its founding in 1872, Alpha has been committed to developing and manufacturing the highest quality specialty materials. For more information, click here.
Suggested Items
Taiyo Circuit Automation Installs New DP3500 into Fuba Printed Circuits, Tunisia
04/25/2024 | Taiyo Circuit AutomationTaiyo Circuit Automation is proud to be partnered with Fuba Printed Circuits, Tunisia part of the OneTech Group of companies, a leading printed circuit board manufacturer based out of Bizerte, Tunisia, on their first installation of Taiyo Circuit Automation DP3500 coater.
Vicor Power Orders Hentec Industries/RPS Automation Pulsar Solderability Testing System
04/24/2024 | Hentec Industries/RPS AutomationHentec Industries/RPS Automation, a leading manufacturer of selective soldering, lead tinning and solderability test equipment, is pleased to announce that Vicor Power has finalized the purchase of a Pulsar solderability testing system.
AIM Solder’s Dillon Zhu to Present on Ultraminiature Soldering at SMTA China East
04/22/2024 | AIMAIM Solder, a leading global manufacturer of solder assembly materials for the electronics industry, is pleased to announce that Dillon Zhu will present on the topic: Ultraminiature Soldering: Techniques, Technologies, and Standards at SMTA China East. This event is being held at the Shanghai World Expo Exhibition & Convention Center from April 24-25.
AIM to Highlight NC259FPA Ultrafine No Clean Solder Paste at SMTA Wisconsin Expo & Tech Forum
04/18/2024 | AIMAIM Solder, a leading global manufacturer of solder assembly materials for the electronics industry, is pleased to announce its participation in the upcoming SMTA Wisconsin Expo & Tech Forum taking place on May 7 at the Four Points by Sheraton | Milwaukee Airport, in Milwaukee, Wisconsin.
Hentec/RPS Publishes an Essential Guide to Selective Soldering Processing Tech Paper
04/17/2024 | Hentec Industries/RPS AutomationHentec Industries/RPS Automation, a leading manufacturer of selective soldering, lead tinning and solderability test equipment, announces that it has published a technical paper describing the critical process parameters that need to be optimized to ensure optimal results and guarantee the utmost in end-product quality.