-
- News
- Books
Featured Books
- smt007 Magazine
Latest Issues
Current IssueBox Build
One trend is to add box build and final assembly to your product offering. In this issue, we explore the opportunities and risks of adding system assembly to your service portfolio.
IPC APEX EXPO 2024 Pre-show
This month’s issue devotes its pages to a comprehensive preview of the IPC APEX EXPO 2024 event. Whether your role is technical or business, if you're new-to-the-industry or seasoned veteran, you'll find value throughout this program.
Boost Your Sales
Every part of your business can be evaluated as a process, including your sales funnel. Optimizing your selling process requires a coordinated effort between marketing and sales. In this issue, industry experts in marketing and sales offer their best advice on how to boost your sales efforts.
- Articles
- Columns
Search Console
- Links
- Events
||| MENU - smt007 Magazine
Rehm's Seamless Handover of Department Management
February 8, 2019 | Rehm Thermal SystemsEstimated reading time: 2 minutes
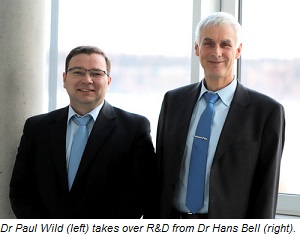
Since February 1, 2019, the research and development department at Rehm Thermal Systems has a new manager: Dr Paul Wild. He takes over as department head from Dr Hans Bell, who has led the research and development department for nearly 20 years and will retire in 2020. Dr Wild has worked for Rehm since the end of 2014.
The previous deputy, Dr Paul Wild, experienced and technologically well-versed, now takes over the management of the development department. "Over the last few years I have been able to familiarise myself with many aspects of the R&D department and accumulate valuable experience. I quickly got involved in the existing development processes and worked with my scientific expertise to expand R&D,” says Dr Wild, who has worked for Rehm, manufacturer of thermal system solutions, since the end of 2014. Dr Bell’s three key pillars of research and development at Rehm will remain the focus for the future: Research projects with institutes and industrial project partners, technological cooperation with customers, but above all internal research and development projects.
After nearly 20 years as head of the research and development department, Dr Hans Bell will continue to work in research and development at Rehm until he retires in 2020, passing on his experience and know-how to assist Paul Wild in meeting the new challenges. "I have great confidence for the future, because the department is in very good hands," says Dr Bell. “Paul Wild has a gift for talking with people, listening to them and leading creative conversations.” He has always felt comfortable "in and with the entire Rehm team," says Dr Bell. "It's a good relationship that is perfectly goal-oriented. For that I’m very thankful.”
To this day, Dr Bell values the work with the customers and project partners of Rehm Thermal Systems: "It is important to maintain a balance between our own development and technological know-how transfer in cooperation with partners.” There’s one thing that makes him prouder than any other: the integration of young people into the company. "Be it students or school pupils who completed internships or undertaking graduate study in development – many have stayed with Rehm to this day. It shows that the company has a really great appeal.”
Dr Paul Wild
Dr Paul Wild studied Aerospace Engineering at the University of Stuttgart. After graduation he worked as a research associate at Hahn-Schickard Institute for Microsystems Engineering in Stuttgart. His specialisation was the reliability analysis of mechatronic systems, particularly based on MID technology. He has worked in the research and development department at Rehm Thermal Systems since November 2014. The main focus of his work is the development and enhancement of thermal systems, as well as technological cooperation with institutes and companies. In 2018 he received his doctorate from Hahn-Schickard Institute on the subject of reliability and life-cycle modelling of solder joints.
Dr Hans Bell
Dr Hans Bell has led the Research and Development Department at Rehm Thermal Systems since 2000. Until the end of 1999 he worked as a manufacturing technologist for DeTeWe in Berlin and was predominantly responsible for production-oriented tasks in the development of connection technologies, particularly soft soldering. During this time he obtained a doctorate from TU Munich, specialising in soldering. Over the course of his career Dr Bell has acquired extensive knowledge in the field of soft soldering, as illustrated by numerous patents, technical papers and books, and lectures and seminars.
Suggested Items
Taiyo Circuit Automation Installs New DP3500 into Fuba Printed Circuits, Tunisia
04/25/2024 | Taiyo Circuit AutomationTaiyo Circuit Automation is proud to be partnered with Fuba Printed Circuits, Tunisia part of the OneTech Group of companies, a leading printed circuit board manufacturer based out of Bizerte, Tunisia, on their first installation of Taiyo Circuit Automation DP3500 coater.
Vicor Power Orders Hentec Industries/RPS Automation Pulsar Solderability Testing System
04/24/2024 | Hentec Industries/RPS AutomationHentec Industries/RPS Automation, a leading manufacturer of selective soldering, lead tinning and solderability test equipment, is pleased to announce that Vicor Power has finalized the purchase of a Pulsar solderability testing system.
AIM Solder’s Dillon Zhu to Present on Ultraminiature Soldering at SMTA China East
04/22/2024 | AIMAIM Solder, a leading global manufacturer of solder assembly materials for the electronics industry, is pleased to announce that Dillon Zhu will present on the topic: Ultraminiature Soldering: Techniques, Technologies, and Standards at SMTA China East. This event is being held at the Shanghai World Expo Exhibition & Convention Center from April 24-25.
AIM to Highlight NC259FPA Ultrafine No Clean Solder Paste at SMTA Wisconsin Expo & Tech Forum
04/18/2024 | AIMAIM Solder, a leading global manufacturer of solder assembly materials for the electronics industry, is pleased to announce its participation in the upcoming SMTA Wisconsin Expo & Tech Forum taking place on May 7 at the Four Points by Sheraton | Milwaukee Airport, in Milwaukee, Wisconsin.
Hentec/RPS Publishes an Essential Guide to Selective Soldering Processing Tech Paper
04/17/2024 | Hentec Industries/RPS AutomationHentec Industries/RPS Automation, a leading manufacturer of selective soldering, lead tinning and solderability test equipment, announces that it has published a technical paper describing the critical process parameters that need to be optimized to ensure optimal results and guarantee the utmost in end-product quality.